Porosity in Welding: Identifying Common Issues and Implementing Finest Practices for Prevention
Porosity in welding is a prevalent problem that often goes undetected until it triggers significant troubles with the honesty of welds. In this conversation, we will certainly discover the crucial elements adding to porosity development, examine its detrimental effects on weld performance, and discuss the best techniques that can be taken on to lessen porosity incident in welding processes.
Common Reasons For Porosity
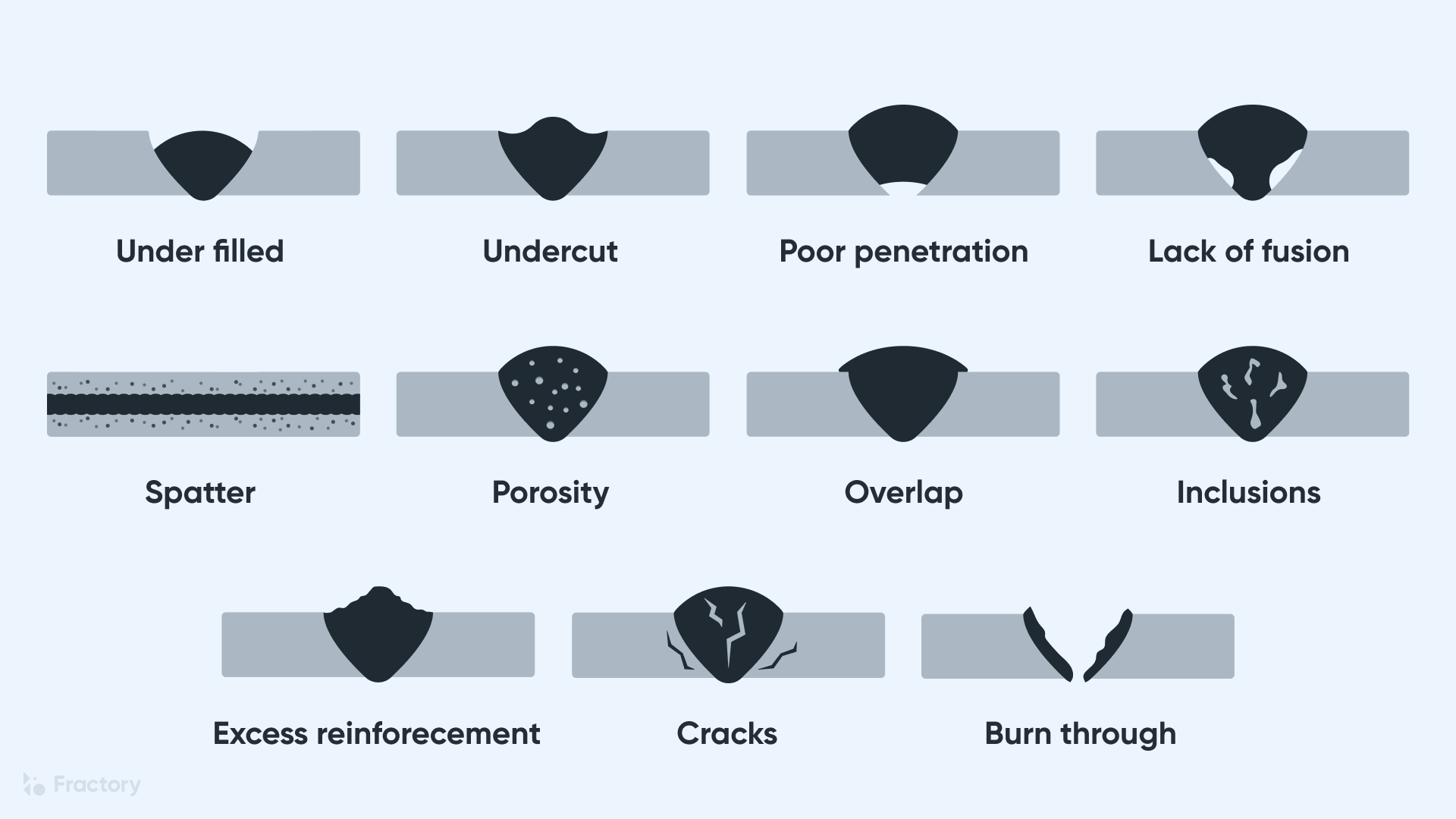
An additional constant culprit behind porosity is the presence of contaminants on the surface area of the base metal, such as oil, oil, or rust. When these pollutants are not properly removed prior to welding, they can vaporize and become caught in the weld, causing flaws. Making use of unclean or damp filler materials can introduce impurities into the weld, adding to porosity concerns. To minimize these common sources of porosity, complete cleansing of base metals, appropriate shielding gas option, and adherence to optimal welding specifications are essential practices in achieving top notch, porosity-free welds.
Influence of Porosity on Weld High Quality

The visibility of porosity in welding can substantially compromise the structural stability and mechanical homes of bonded joints. Porosity produces voids within the weld steel, compromising its total strength and load-bearing ability. These voids work as tension focus points, making the weld a lot more prone to breaking and failure under used loads. Furthermore, porosity can reduce the weld's resistance to rust and various other ecological factors, better lessening its durability and efficiency.
Welds with high porosity levels tend to exhibit lower influence stamina and decreased capability to deform plastically prior to fracturing. Porosity can hinder the weld's capability to properly send forces, leading to premature weld failing and prospective security threats in important frameworks.
Finest Practices for Porosity Avoidance
To boost the architectural stability and quality of welded joints, what specific measures can be applied to lessen the incident of porosity during the welding process? Porosity prevention in welding is vital to make certain the honesty and toughness of the last weld. One reliable practice appertains cleansing of the base read the full info here steel, getting rid of any kind of pollutants such as corrosion, oil, paint, click this link or moisture that could result in gas entrapment. Guaranteeing that the welding tools remains in good problem, with clean consumables and ideal gas flow prices, can additionally substantially lower porosity. In addition, keeping a stable arc and regulating the welding parameters, such as voltage, existing, and take a trip rate, helps create a regular weld pool that decreases the danger of gas entrapment. Using the right welding technique for the details material being welded, such as readjusting the welding angle and gun position, can better avoid porosity. Routine assessment of welds and prompt removal of any concerns recognized during the welding process are essential methods to avoid porosity and create high-grade welds.
Importance of Proper Welding Techniques
Carrying out proper welding methods is paramount in making sure the architectural stability and quality of welded joints, building upon the foundation of effective porosity prevention actions. Extreme warmth can lead to enhanced porosity due to the entrapment of gases in the weld swimming pool. In addition, utilizing the ideal welding specifications, such as voltage, current, and travel rate, is vital for achieving audio welds with very little porosity.
Moreover, the choice of welding process, whether it be MIG, TIG, or stick welding, should straighten with the certain demands of the project to guarantee optimal outcomes. Appropriate cleaning and prep work of the base steel, as well as selecting the best filler product, are also vital elements of efficient welding strategies. By sticking to these finest practices, welders can decrease the danger of porosity formation and produce premium, structurally sound welds.

Examining and Quality Assurance Measures
Examining procedures are crucial to discover and prevent porosity in welding, ensuring the strength and resilience of the final item. Non-destructive testing approaches such as ultrasonic screening, radiographic screening, and aesthetic evaluation are typically utilized to identify potential issues like porosity.
Post-weld assessments, on the various other hand, evaluate the final weld for any type of flaws, consisting of porosity, and confirm that it satisfies defined standards. Implementing an extensive top quality control plan that includes complete screening procedures and inspections is vital to lowering porosity problems and guaranteeing the general high quality of bonded joints.
Final Thought
To conclude, he said porosity in welding can be an usual issue that influences the top quality of welds. By determining the usual reasons of porosity and executing best methods for prevention, such as correct welding methods and testing actions, welders can guarantee premium quality and trusted welds. It is essential to focus on prevention techniques to decrease the incident of porosity and keep the stability of bonded structures.